This black 02 coating has been specially developed for the internal moving parts of watches (rough movements, weights..) and their specific constraints: handling, stone setting, engraving and other finishing operations.
PHYSICAL VAPOR DEPOSITION (PVD) – PROCEDURE
PVD (Physical Vapor Deposition) is a metal deposition coating process that allows thin films of material to be deposited under vacuum using vapor.
For PVD coating the deposition temperature is usually between 80 and 150°C.
The deposit thickness is 1.5 +/-0.5 (micron)
HV 0.05 hardness is between 800 and 1000
Conforms to REACH and RoHS standards
Applications
Black 02 colorized coatings
- Flanges
- Bridges
- Plates
- Oscillating weights
- Screws
- …
The advantages
- Excellent quality for money
- Excellent results in watchmaking tests (climatic resistance, UV, ..)
- Gloss, satin or matt black color depending on the substrate
- Black PVD can be deposited on all substrates (copper alloys, titanium, gold, steel and stainless steel, plastics)
- Clean deposit
- Good compromise between ductility and hardness
- Homogeneity and reproductivity of the color
- Homogeneity and reproductivity of thickness
- Resistance against climate and UV
- Low temperature procedure
- Respect of terminals
- A black PVD treated part can be detreated and retreated
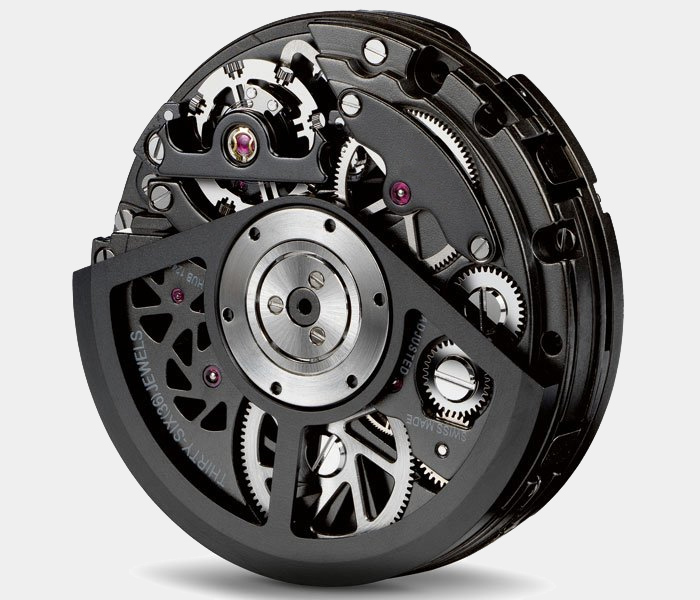