The barrier layer coating has been specially developed for movement parts made from materials that are prone to corrosion such as copper alloys and carbonated steels (rough movements, weights, etc.).
This extremely thin barrier layer performs better than a 1 µm galvanic nickel layer.
This barrier layer is combined with a decorative PVD coating (black, blue, gilded, rhodium…) with a standard thickness between 1 and 1.5 µm.
Only one ebauche reference whatever the coloring.
Validation of the barrier – Independent laboratory
Validation of the barrier layer (Dubois Laboratory)
- Equivalent to a 1µm galvanic nickel layer
- Humid heat tested according to NIHS 96-50 standard
- Salt spray tested according to ISO 9227,
- Sulphur compound tested according to ISO 4538 (thioacetamide)
Atomic layer deposition (ALD) – Procedure
ALD is a composition of thin films of the type CVD (Chemical Vapor Deposition).
The principle consists of exposing the surfaces to gas pre-cursors so as to obtain thin films. The deposit is self-regulating and takes place cycle after cycle. Once a film of atoms is deposited, the deposition stops itself. The following cycle begins once the previous one is finished.
For ALD coating the deposition temperature is usually 150 °C.
Conforms to REACH and RoHS standards.
Applications
- Flanges
- Bridges
- Plates
- Oscillating weights
- Screws
- Etc
The advantages
- Excellent quality for money
- All-in-one: barrier layer + decorative deposit
- Simplification in the number of ebauche references
- Improved resistance against corrosion
- Dry coating method
- Clean industry
- The barrier layer can be deposited on all sensitive substrates
- Excellent homogeneity on 3D parts
- Respect of terminals
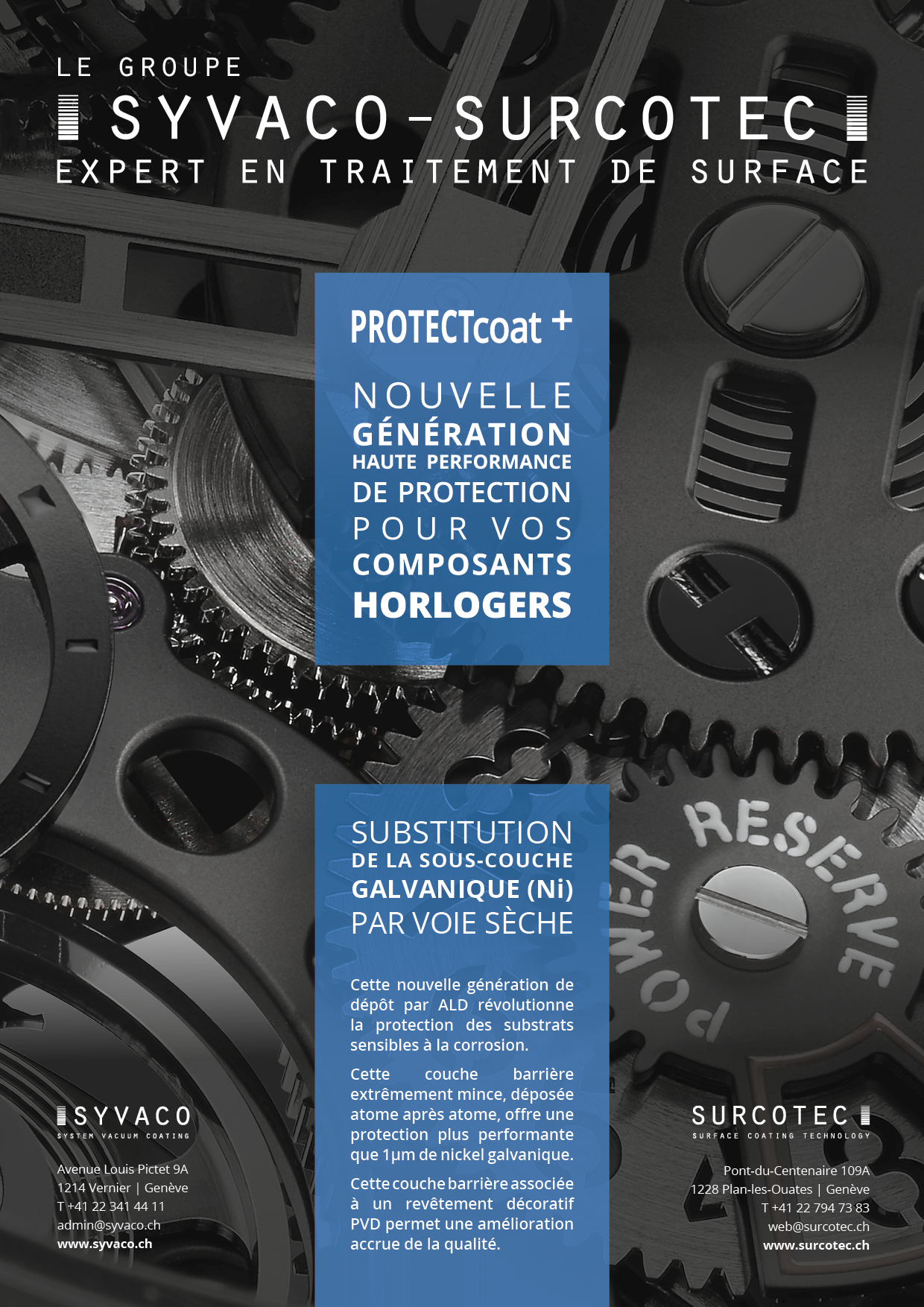
BULLETIN SSC N°88 DÉCEMBRE 2019
A coating obtained by Atomic Layer Deposition (ALD) as a replacement for galvanic layers for the protection of timepieces…
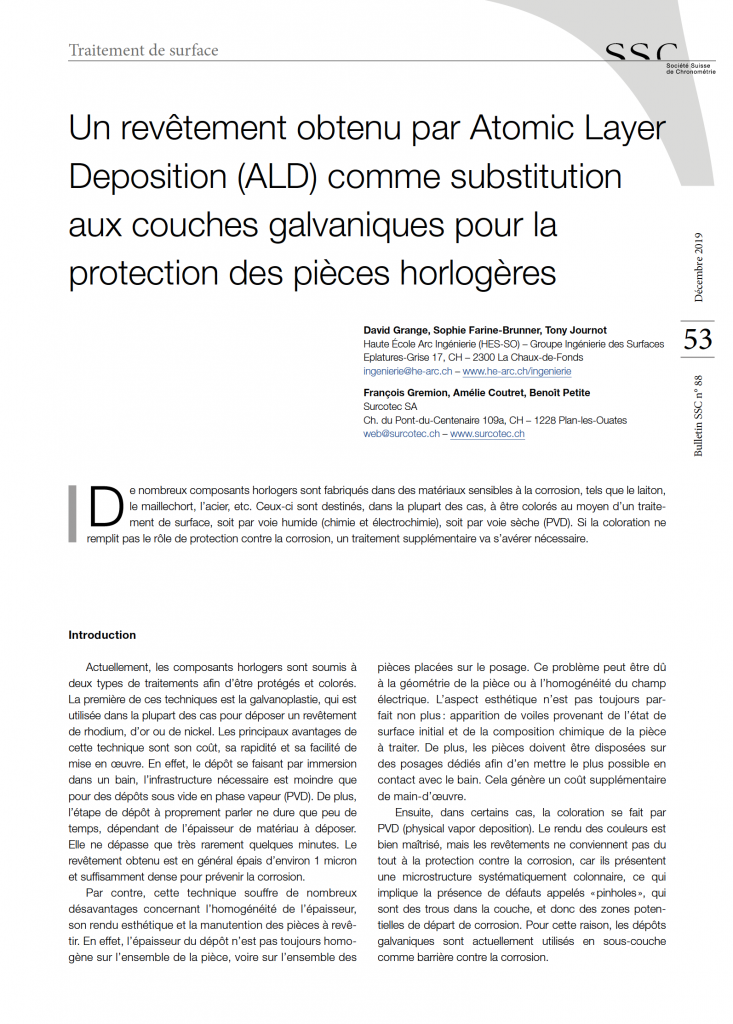